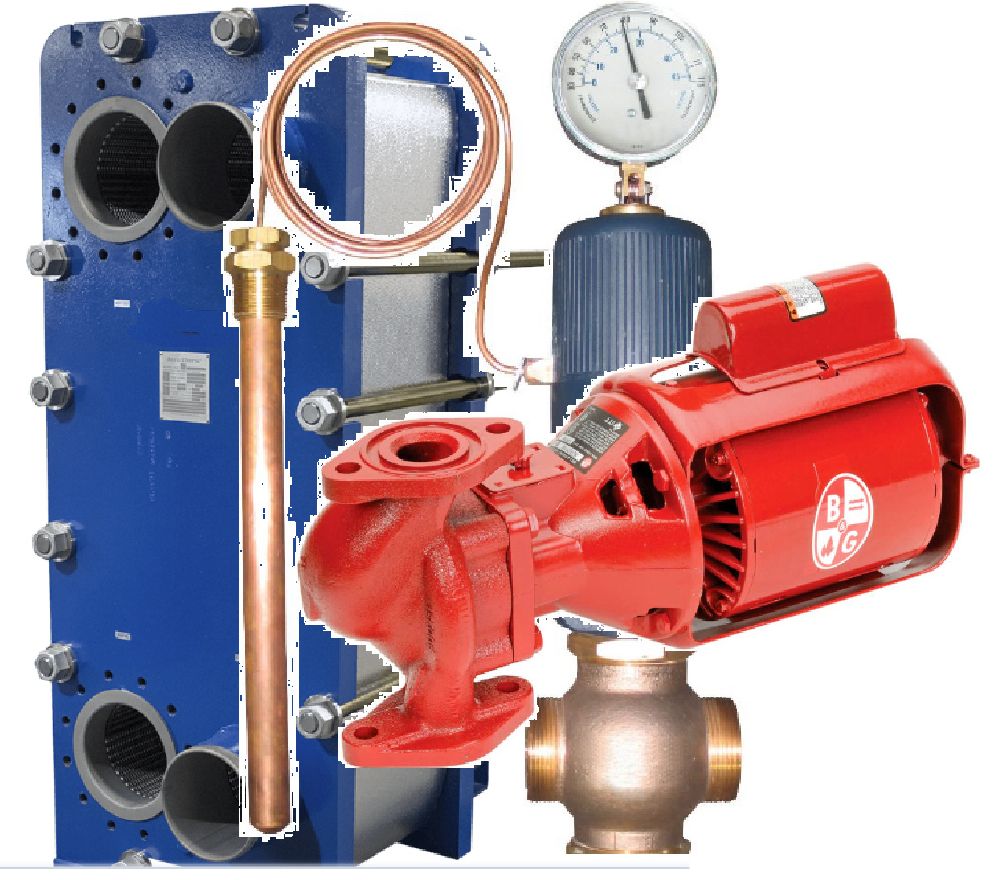
In todays AI world, it is tempting to believe that computers are the answer for everything. I can assure you that CHAT GPT only spits out the collected ignorance of the masses. That is why it is such a good match to what they think. In real processes like die casting, the laws of physics trump any sugar coated theory dumped out of AI. As we develop new technologies like 3D printed conformal cooling we need to focus on getting the hardware right before we try to computerize it.
Yes you can spend a lot of money on computerized thermal control equipment. If the physics is not right the castings will not turn out any better. I prefer to build up from a solid foundation,
K (keep) I (it) S (simple) S (stupid)
City tap water is one of the more cost effective heat transfer fluids
- Great safety data sheet
- Not messy
- Double the heat transfer capacity of hot oil
Gravity
- Has not failed us yet
- A tank above the die is the easiest way to insure that the passages in the die are filled with fluid instead of air
Visual management
- fouled heat exchangers result in a cloud of steam at the exit
- A visual waterfall into the tank shows that the pump is running circulating fluid in the die
Minimalist
- More components add cost and down time
- A bulb actuated temperature control valve is as effective as a thermocouple, controller and solenoid valve
- A simple 110V AC pump run by a switch is very cost effective circulation
- A50 psi check valves on the tank return line keeps water over 100C from boiling until after it is cooled below 100C by the heat exchanger
City water works well as a heat transfer fluid. This assumes that you keep it pressurized while it is in contact with die steel above 100C so no boiling occurs. Boiling results in deposit formation. Die steels usually must remain above 80C to make good castings. It is easy to overcool critical die sections by circulating tower water at 25C through the passages. 80C city water in an isolated loop insures that related die sections are not overcooled.