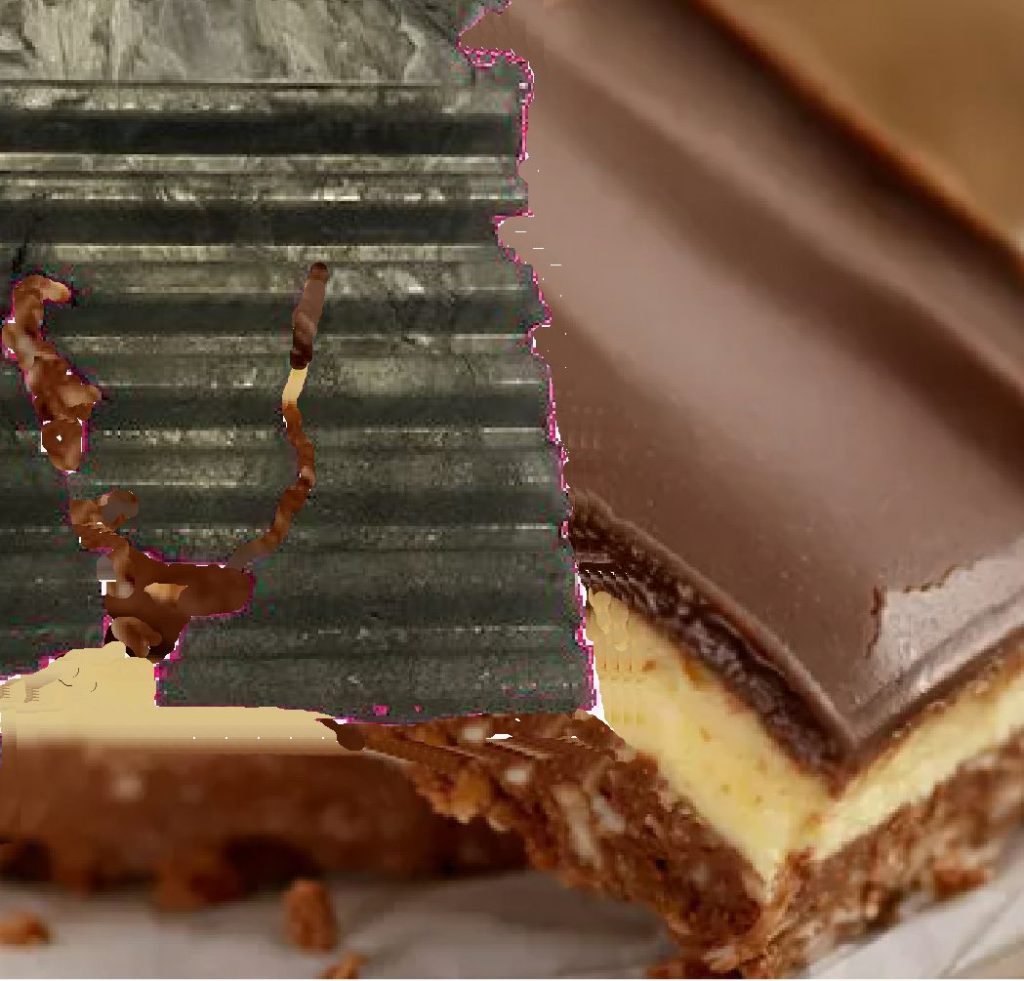
When you are choosing materials to create a chiller block- more heat conductivity is better. Beryllium copper has 5 times the heat conductivity of H13. Fast freezing of the aluminum creates the crumbly shut off that makes chill vents work. Somewhat messy as the leading crumbs fill the casting machine pit. When choosing the main insert material, more heat conductivity may not be better. Most customers do not wish to buy crumbly parts. Otherwise we would make all of the inserts out of beryllium copper. Fortunately H13 has poor conductivity. It makes it possible to get the molten metal to the far side of the mold before it freezes. Interestingly a thermocouple drilled into a H13 insert to 6mm from molten metal does not rise in temperature until almost one full cycle time has elapsed.
A few proponents of conformal cooling have chosen to over simplify. A die does not run faster simply because more is better. Quickly making good quality parts occurs when proper choices are made. In a 390 alloy (740C cast temp) valve body heat is a problem. An Anviloy ( 3 times the conductivity of H13) roto pocket sub insert proved to be more effective than a conformal cooling sub insert. ( Having tried both) The scale in the water passages of the Anviloy sub insert could be drilled out each run such that the casting quality did not deteriorate with die age.
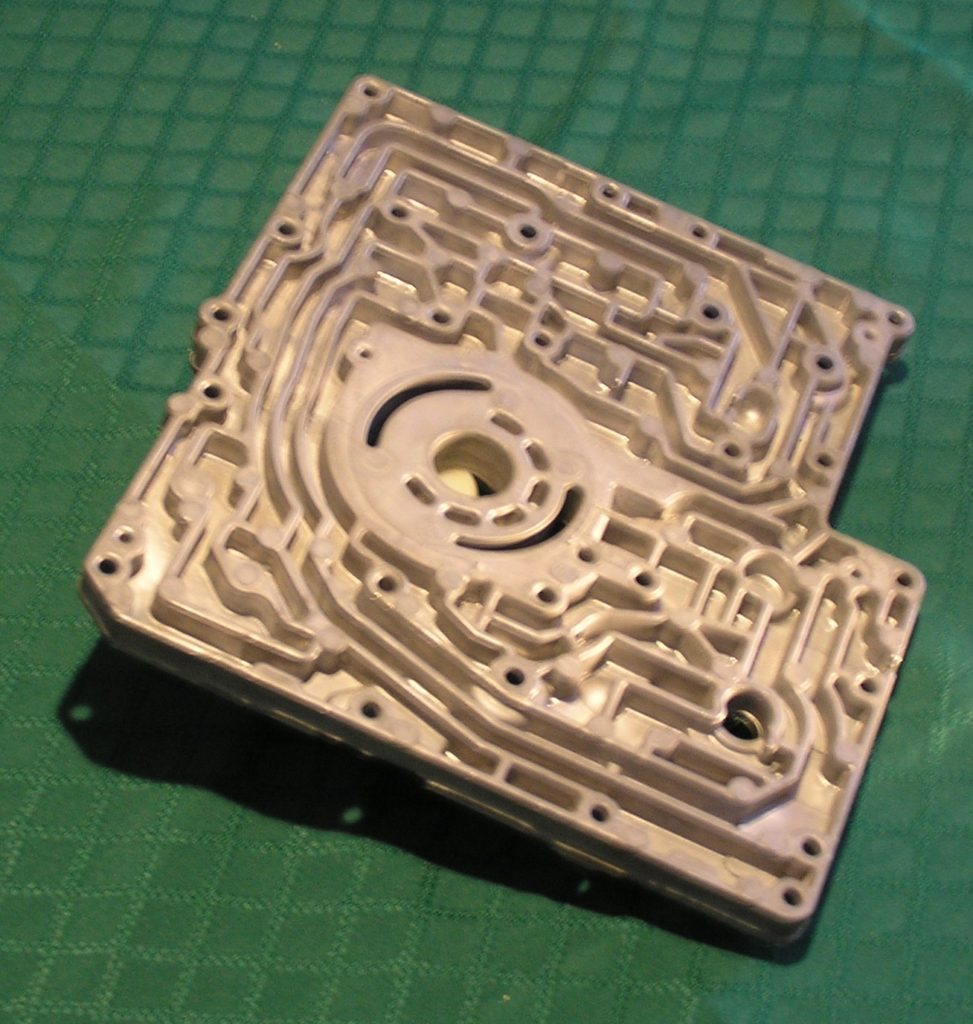
However I believe more is better when it comes to the Nanaimo bars that my Canadian wife makes for me. I can even put up with the fact that they crumble.