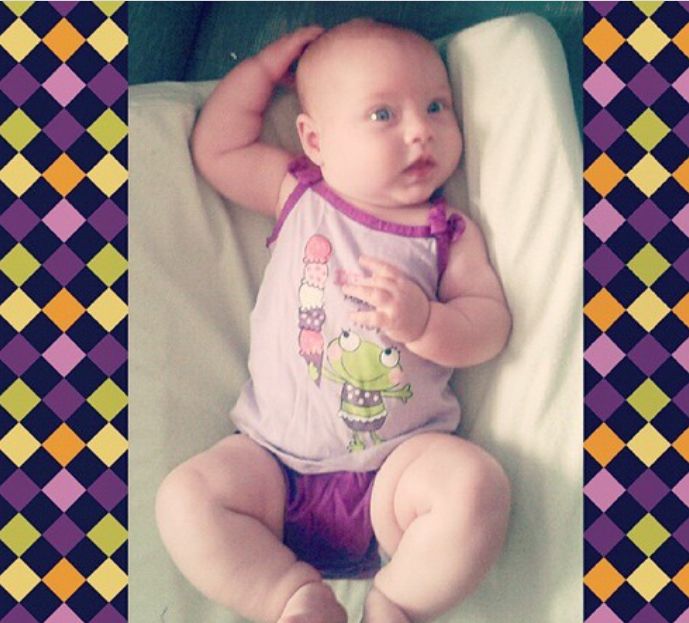
We discover that our two hands can be simultaneously doing different tasks at a young age. This seems to be forgotten when many die cast cells are set up. Yes it is easier to plan a process in a sequential manner. Unfortunately it is difficult to be competitive when the casting cell operates in a sequential fashion.
Early in my career I was charged with automating an entire plant. This plant specialized in making some of the most difficult castings in the game. In most cases it was necessary to achieve the same cycle time that the best cast operators could achieve to make good quality parts. This forced me to micro analyze how a manual die caster could beat the robots. It turned out that they learned how to jump the gun
Running an automated die casting cell is about synchronizing the moving elements.
Die Cast machine clamp — Shot — Die — Extractor — Ladle — Spray robot
It is difficult to win a relay race if you wait every time that you are supposed to pass the baton.
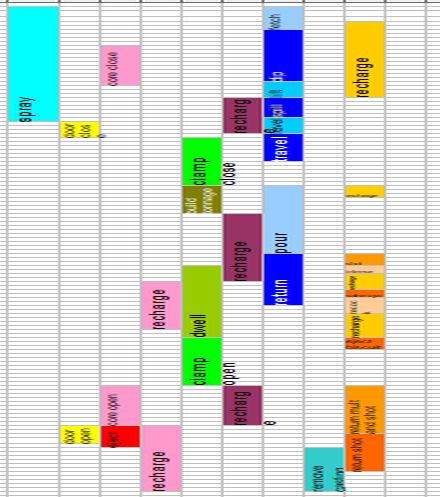
- Pretip of the ladle cup and pouring directly into the sleeve starts at die face touch results in the pour half complete at die lock and no wait for metal run to complete down the launder.
- Subcore pulled at end of dwell
- Slides open during die open
- Extractor reaches through a window in door starting 4 inches before die full open (I leave both doors closed)
- Sprayer partially advances during extract
- Slides close during spray
- Sprayer completes return home during die close
- Subcores close during pour
In this era of Mega presses, automated casting cycle time is even more critical to realizing a profit. It is also fortunate that casting quality improves with reduced cycle time as long as the dwell and spray time is unchanged. As you look at your own casting operation be aware that some of your competitors understand parallel action.