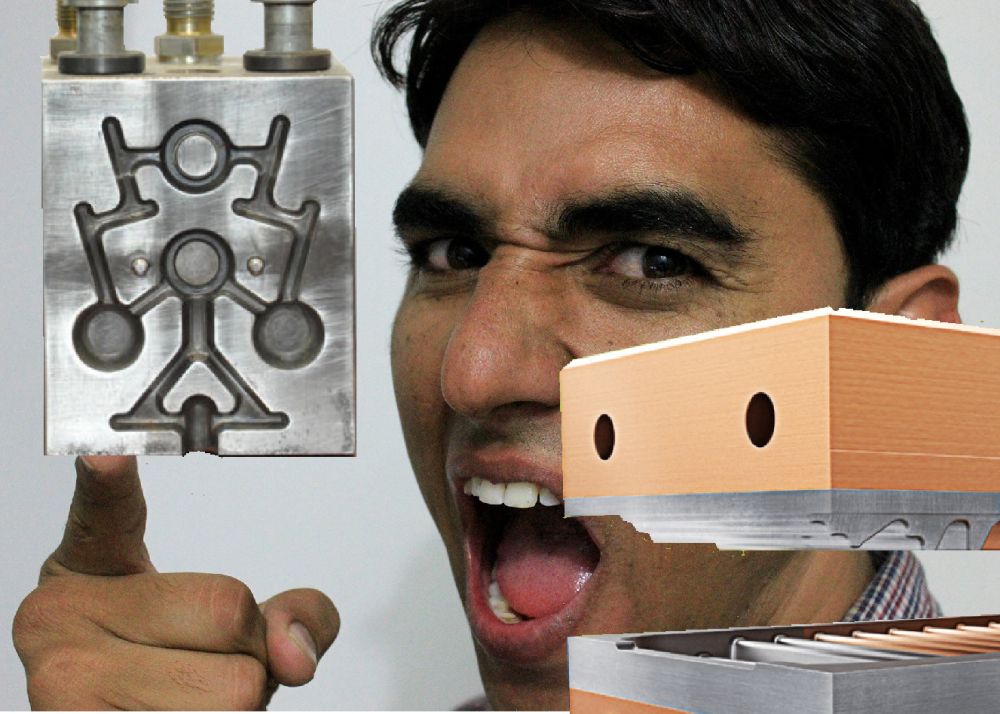
The die casting engineer is at the receiving end of customer venting when part quality suffers due to a lack of venting. Virtually all aluminum die castings dies require venting. This is related to the vaporization of the organic release agents used. These agents vaporize when the aluminum fills the cavity creating a gas barrier between the molten aluminum and the mold. This vaporization creates 500 psi (34 bar) gas pressures at the middle of the fast shot event. Vacuum can reduce that pressure by 15Psi (1 bar) but does not eliminate the need for rapid venting.
Vent elements with moving valves have a greater flow rate when open. This style is less popular because the larger flow rate is lost because the start of valve close must be triggered early to insure that the valve is closed before the molten metal arrives. Waffle style vents are the most popular. The lack of moving parts improves their reliability. The biggest challenge is choosing vent materials that resist exposure to molten aluminum without wear or soldering. As our industry develops a successful formula for structural body castings we see an evolution away from vacuum to waffle plates that are double the historic size and have H13 inserts for the first few waffles. This is related to the fast (6 m/s) fill speeds and hot metal temperatures. Thin wall castings with long fill path lengths use faster shot speeds like the big magnesium dash panel frame castings.