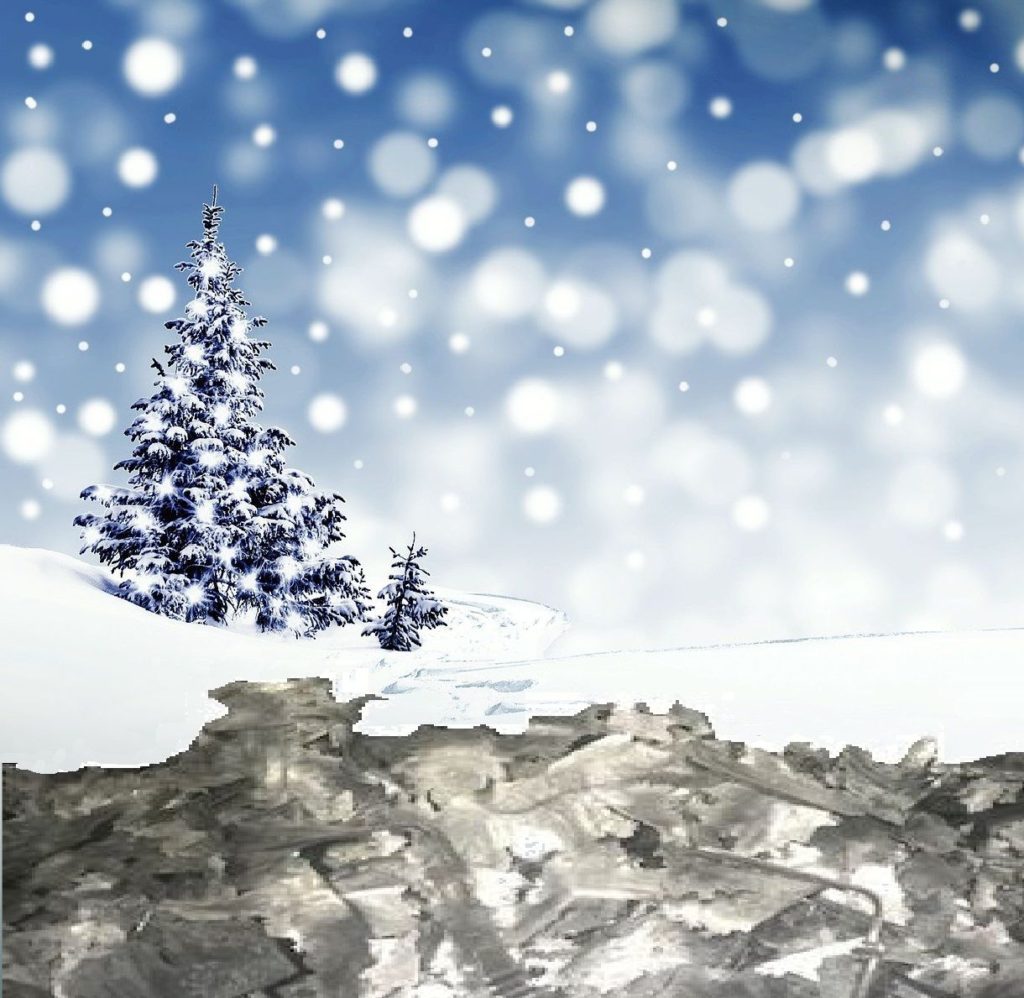
Snow for Christmas day like we had this year is wonderful. It makes the world seem clean and bright. “Snow” inside a die cast plant just makes a mess. Yes we all know that die cast dies require venting to work properly. The trick is to vent out the gas without venting out the aluminum. It is the vented aluminum that we in the die cast community call “snow”
For those practitioners who have not invented a strategy for controlling snow, it is discovered after the die is put into service. At that point in time the production demand for parts prevents implementing proper fixes. Been there. Just because it is not possible to completely fix the die at that time, doesn’t mean that it is not possible to do something to get better results. In all cases vent features on the die increase the frontal area of the molten metal. The applied pressure multiplied by the frontal area determines the tonnage required. It really starts to “snow” when the applied pressure exceeded the tonnage of the machine because the die blows open. Die vents need to be attached at the last place to fill. Do a short shot to determine where that is. Vents attached to earlier places in the fill only bleed off metal that should have been available to fill porosity at the far end. In many cases a line of weld can block these off or undercuts can stick the overflow into the die filling the unneeded vent.
Every cavity replacement for dies prone to “snowing” includes a redesign of the vent system. Waffle style vents achieve vent path shut off using less frontal area. Zig zag vent shut off works for other dies that are not as close to consuming the available machine tonnage. The knowledge gained from this Kaizen activity makes it possible to launch “snow” free new jobs out of the box.