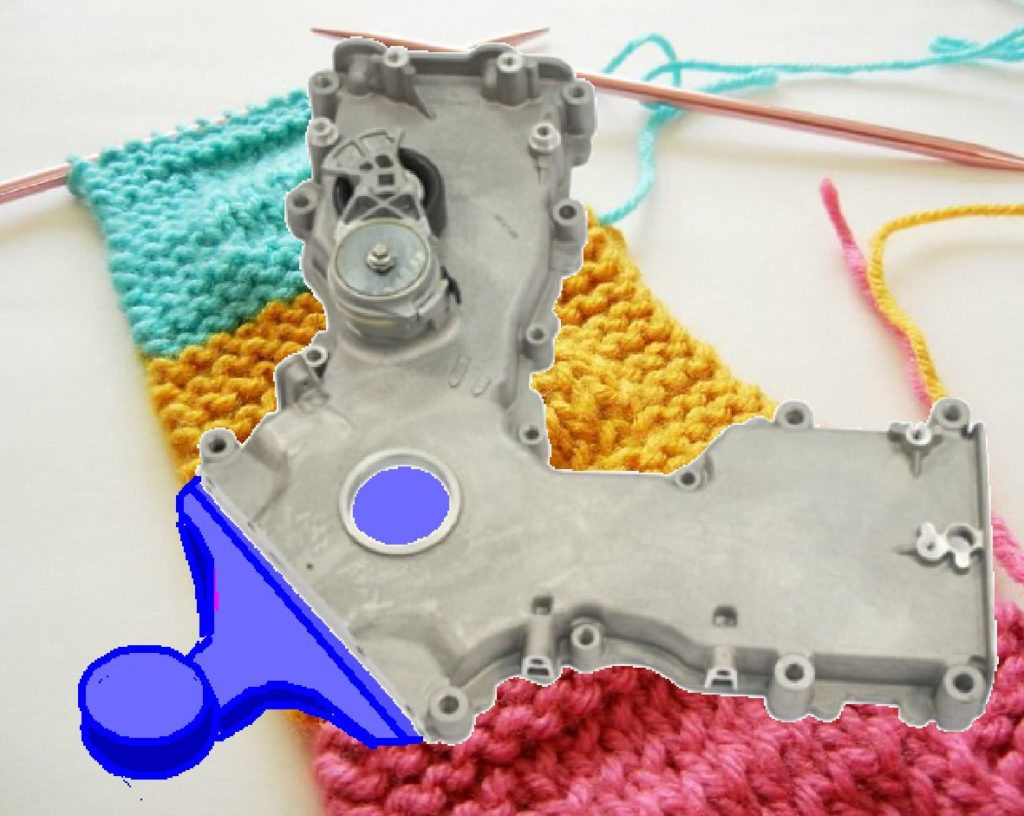
A weakness in a casting caused by molten streams of metal incompletely joining back together. In actual castings knit lines result in leaks in pressure tight castings or tears in structural castings. A common cause of knit lines is multiple gate inlets. Part geometry and/ or a desire to use trimmable gates (thickness less than 3mm) cause high pressure die cast designers to use multiple inlets. For critical castings, knit lines result in downstream quality sorting such as 100% pressure testing or die penetrant testing.
When both casting and machining are contracted together other options are possible. The pictured front engine cover was made using a continuous single gate. To obtain enough gate area this gate was thicker than the 3mm maximum that enables a conventional trim without break in. A crop was used to remove the gate. This was a pair of 8 inch cylinders in both top and bottom halves of the trim.The cylinders push at each other after the trim die closes and trims the rest of the perimeter. The disadvantage is that a 3mm gate projection remains. Not a problem for the milling cutter in this case.
The hole for the crankshaft was also filled in. An extra cutter was incorporated into the boring tool to handle the trim projection in this area.
It is always more effective to engineer out defects. The lack of knit lines in this design eliminated the normal pressure test. I can assure you that even 100% pressure testing will not catch all the leakers.