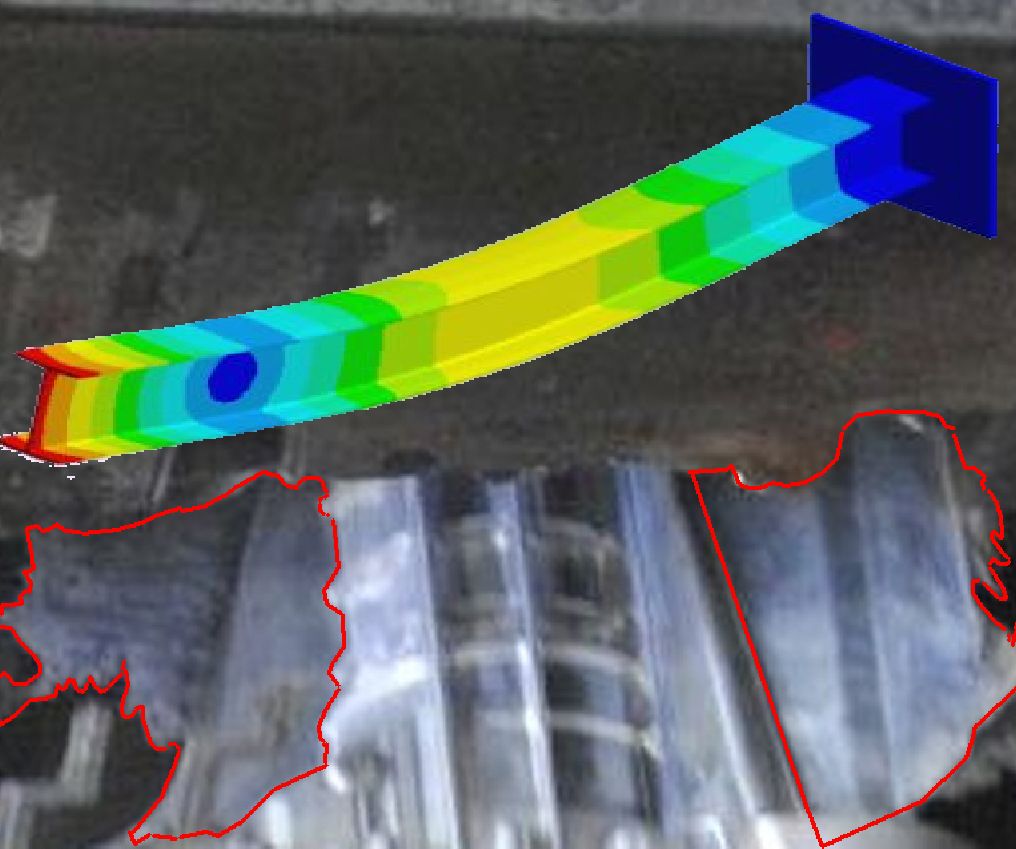
One of the early lessons taught to mechanical engineers is that materials deflect under applied loads. I can assure you that there is no shortage of applied loads in high pressure die casting. I thought that a 1000 ton press was massive as a new die cast engineer. Now we see 10,000 ton high pressure die casting presses. When you see the blocks of steel used to make high pressure die cast platens, it is hard to picture them flexing
This discussion is about the flexing of the ejector platen. On a 400ton die casting machine you can pretty much ignore ejector platen flexing. The ejector die itself is rigid enough to bridge across the platen face. On a 4000 ton die cast machine platen flex is an important consideration. The style of clamping mechanism is also a factor. There are four common styles.
Vertical pin axis book links
Horizontal pin axis book links
4 corner links
Hydraulic cylinder 2 platen
It is usually necessary to design the ejector die to match the style of machine clamp. Dies run in machines that they were not designed for are well known for flashing.
Large dies with slides will flash. Even if you are able to blue the die to shut off at steady state temperature, the first shot is not at steady state. Die require 30 to 100 shots to reach steady state even with preheat. Properly designed dies eject all flash every shot. This avoids die damage related to closing on flash. Remember the machine could be applying 10,000 tons on a small piece of flash