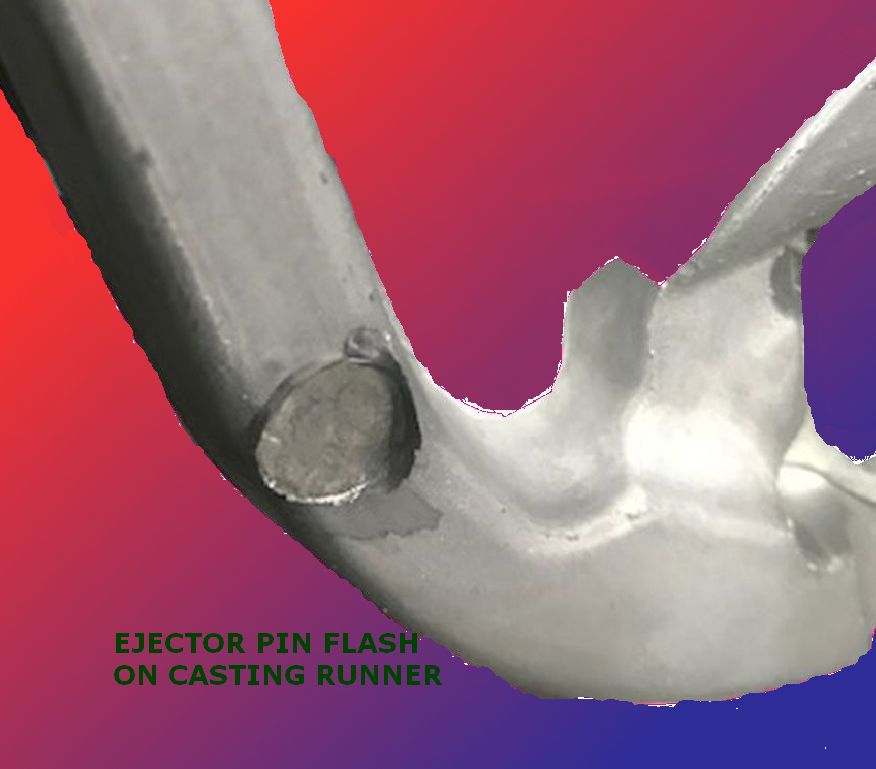
We have all been there. Customer quality complaints cause us to jack up the fast shot speed and final metal pressure. Metal is forced into the gaps and showers out of the die like snow. As die casting engineers this is a problem we fight with. None of us enjoy cutting our fingers on the sharp flash edges.
Ejector pins are known to have undesired flash rings. In many cases a hand deburring operation is needed to remove this flash. The tendency of ejector pins to exhibit flash is related to a law of physics called running fit. It is necessary to have a gap around an ejector pin for it to move. The size of the required gap increases as the diameter of the ejector pin increases. This is why larger ejector pins are more likely to have flash rings. Most diecasters avoid using pins larger than 1/2 inch because they are sure to flash.

Historically it was necessary to learn and understand the guidance given in the machinery handbook to calculate running fit. These days you can find handy calculation assistance online. In the example pictured about a 160mm shot tip requires a .003 gap minimum. This is a lot larger than the gaps normally used to control ejector pin flash. This also explains why larger shot tip diameters limit the maximum metal pressure that can be applied. It is very easy to spray metal out sleeve when using a conventional designed 7 inch dameter shot tip at the desired 15,000 psi final metal pressure. As our industry attempts to design for 6000 ton 200 lb castings with a 10 inch tip, the engineering challenge will be creating a shot tip design that holds the pressure without flashing.