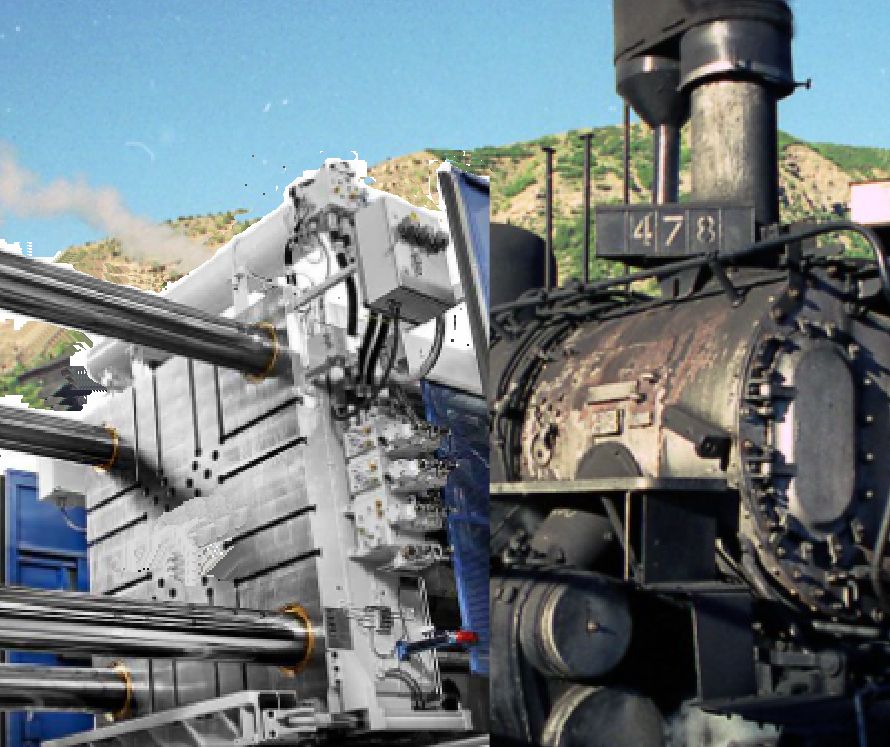
High pressure aluminum die casting is a thermal process. Our melt furnaces add a lot of heat to make aluminum molten. During each casting cycle this heat is transferred to the casting die solidifying a casting. In each casting cycle the heat added to the casting die must be removed so that the die is ready for the next casting event. Evaporation of water is the most common heat removal method. Die spray systems and cooling towers remove this heat Because the thermal conductivity of die steel is low the majority of the heat is removed by die spray when it is used. This article is focusing on the heat removed by the thermal passages within the die
Fluids flowing through the thermal passages in the die remove heat. Cooling tower water is the most commonly used fluid because water has a high heat transfer capability. Other fluids used are hot oil or compressed air. The properties of aluminum castings are enhanced by rapid cooling. In many casting dies careful placement of internal thermal cooling passages is needed to create quality castings. These dies only produce quality castings when proper heat transfer flow occurs through clean passages.
Cooling tower water has some disadvantages. The evaporative cooling tower concentrates minerals in the water. These minerals then deposit within the casting die as scale. I always use individual return lines so that a once a shift check for plugged thermal passages can occur. Visual management is better than nothing, but it can result in whole shift of scrap castings. No heat removal is occurring if the passage is plugged with scale. It is even more frustrating when you need to pull the die once per shift to clean out scale build up -happens when boiling occurs in the passage.
The emergence of structural castings and 3D printed conformal cooled inserts is causing a rethink. Some players are trying to set up a HPDC process more like injection molding. ( The die temperature is totally set by the TCU (thermal control unit) More internal die cooling is designed in to eliminate the evaporative spray cooling. As with any new technology being developed there are growing pains. Scale build up being one of them. Starting my career as a piping engineer I suspect the solution for scale build up will come from our “Engineering” roots. Engineers are the people who ran the steam locomotives. Eliminating scale mineral buildup is a lot easier if you circulate water that does not contain them. Sounds like boiler feed water .https://en.wikipedia.org/wiki/Boiler_feedwater
Having made a few million aluminum castings without using evaporative spray cooling, I can report some benefits. The casting plant is no longer a steam bath in the summer. Spray lube induced porosity problems disappear. Beyond that there is a fresh water shortage .https://www.bbc.com/future/article/20170412-is-the-world-running-out-of-fresh-water