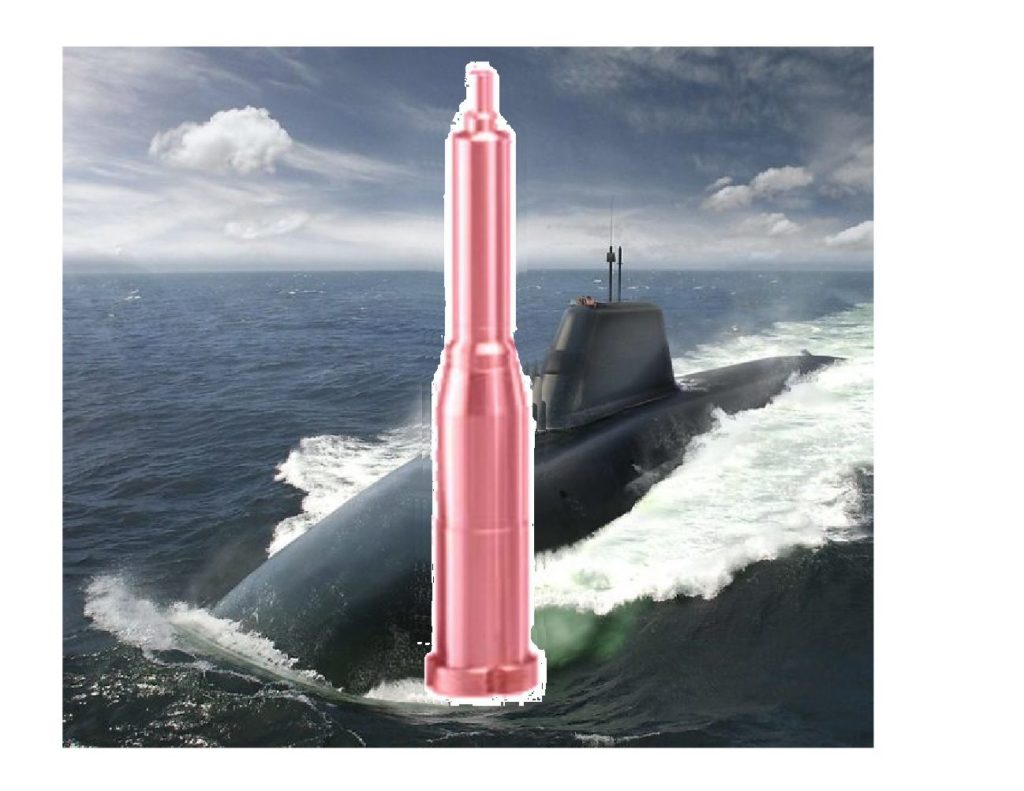
Many real castings require cast holes that are not aligned with the mould direction. If the feature can be created on a pin that is less than 60mm in diameter, a subcore is a good design choice. This is especially true if axis of this core needs to be skew; Many die casters struggle with subcores because they are not as easy to operate as regular core pins
ISSUES
- HEAT REMOVAL
Subcores are effectively separated from the die insert thermal passages. My subcores have 25mm rear diameters such that they contain a cascade The subcore cycle is timed to pull the core out of the casting as soon as possible. I add a second PLC to run the cores when faced with operating a casting machines with OEM program locks
2. LUBRICATION
The subcore quickly seizes to the operating bushing if the running gap is not lubricated. Installing a pressurized lube pump to force grease into the gap only results in stained castings. The back side of my running fit is atmospheric vented. My lube reservoir in the die is filled once per day
3. SEIZING
I have not been able to eliminate the wear that causes a subcore to seize. My designs enable quick removal of a seized subcore and bushing without die removal. The bushing is 2/3 pre split on the back side to make removal and recovery of the subcore pin easier
4. BLOW BACK
Some brands of die cast machines do not maintain core hydraulic pressure during the shot. I manifold mount pilot check valves directly on the subcore cylinder to fix this. Even though many die cast machines come with pilot checks on the machine core valves, the hoses balloon too much for this to prevent core blow back. The sandwich D03 pilot checks that I used are rated for 5000 psi (350 bar) I normally pair a cylinder mounted pilot check with a cylinder that is also rated for 5000 psi. This combination enable use of the full 5000 psi holding pressure even when the machine only delivers 2000 psi.