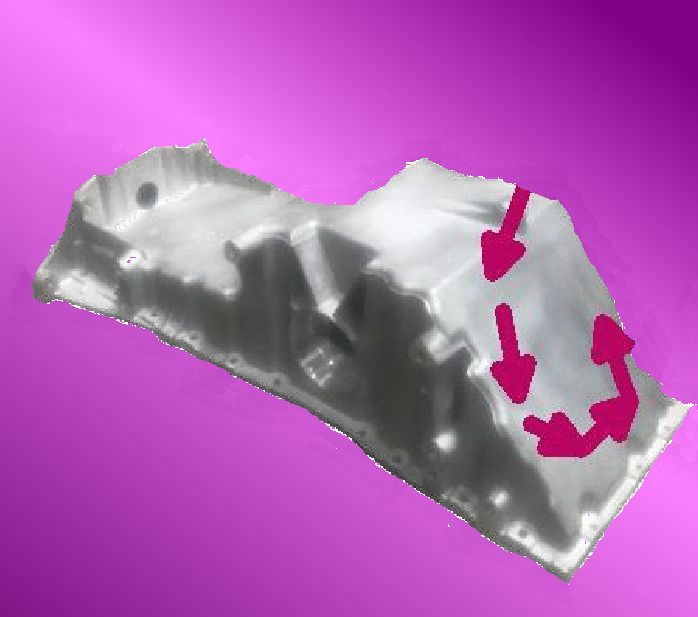
Success- The runner system run through the flow model software finally showed that the vents were the last place to fill. —– Not so fast —- Many real castings will deviate from the predicted fill when the die is actually run. Swirl is a common item to correct as the parts we try to make are thinner and flatter. Swirl is a fill pattern where the incoming metal travels across the part and back effectively doubling the fill travel length.
Oil pans are known to be susceptable to swirl. Swirl in filling an oil pan casting usually results in partially bonded knit lines that are known to leak.
I still recommend tuning the runner design until a flow model shows a swirtl free fill pattern. In many cases this saves massive gating changes that only can be implemented with major amounts die life spoiling welding. In the example shown the swirl we saw on the first casting was eliminated by simply adjusting the shape of the gate fans. The fill pattern after adjusting now matches the pattern we saw in our flow models. I am hopeful that the accuracy of the models can be improved such that gate shape adjusting is no longer required after real castings are made.