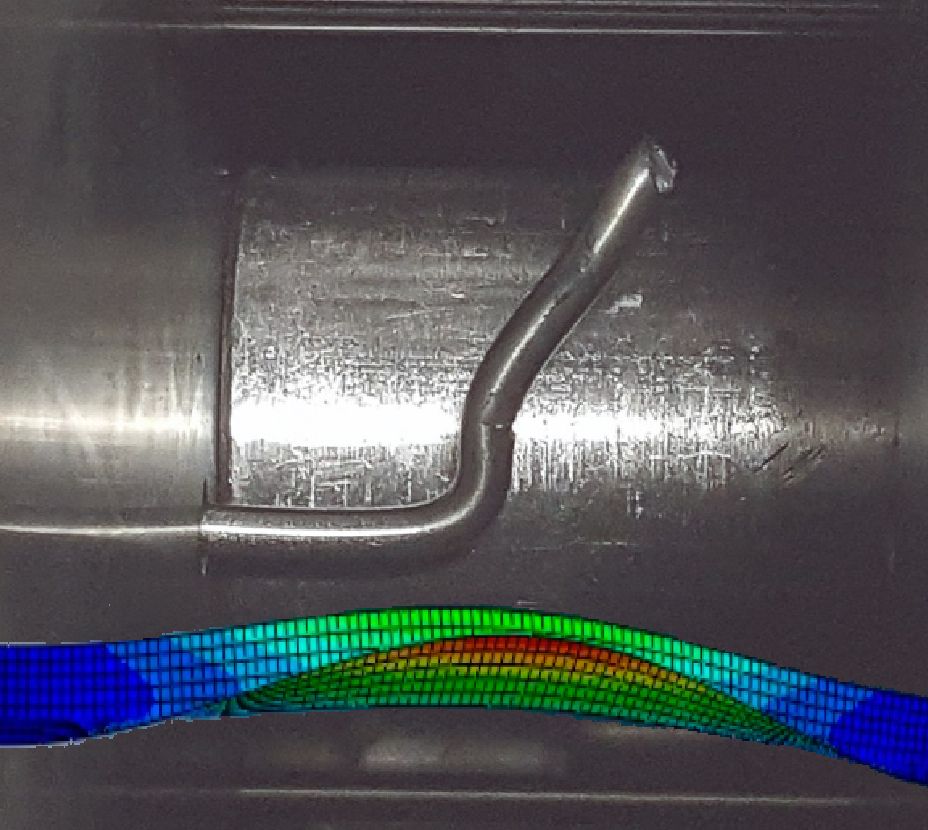
Creating a high pressure casting die design for the new 8000 ton machines would be a lot easier if you could just upscale a die design for a 4000 ton machine. The ejector pins would have twice the diameter and length. Unfortunately they would also have twice the sliding fit gap. Molten aluminum has the same properties independent of machine tonnage. It happily penetrates gaps that are twice as large. Aluminum in the gap around ejector pins effectively seizes them. This limits the maximum ejector pin diameter when casting 380 alloy to 11mm. Less fluid primary alloys like 356 can work with pins up to 15mm diameter.
Ejector pins in 8000 ton dies must deliver the same force per pin as pins in 4000 ton casting dies. Because buckling limits the maximum force that a pin can deliver. They cannot be longer than the pins used in a 4000 tin die. This strategy works well for the 8000 ton castings with shallow relief. Taller parts require more complicated designs to keep the ejector pins from buckling.
I like the position to win strategy used by Bear Bryant football coach of the University of Alabama. Because heat check increases the force on ejector pin, a pin that worked on a new die will buckle unexpectedly. Adding set screws to enable rear removal is no help whatsoever. Rear set \screws only work removing unbent pins (never the case) Whats worse is the replacement pin will buckle again almost immediately because the heat check that caused the pin failure is still there. Getting back to position to win. I initially drill the ejector pin clearance holes in the holder for threading such that a brass head hex head bolt can be easily added as a guide bushing. A column guided in the center can deliver 4 times the force. Good die designs have features that enable quick compensation for wear issues.