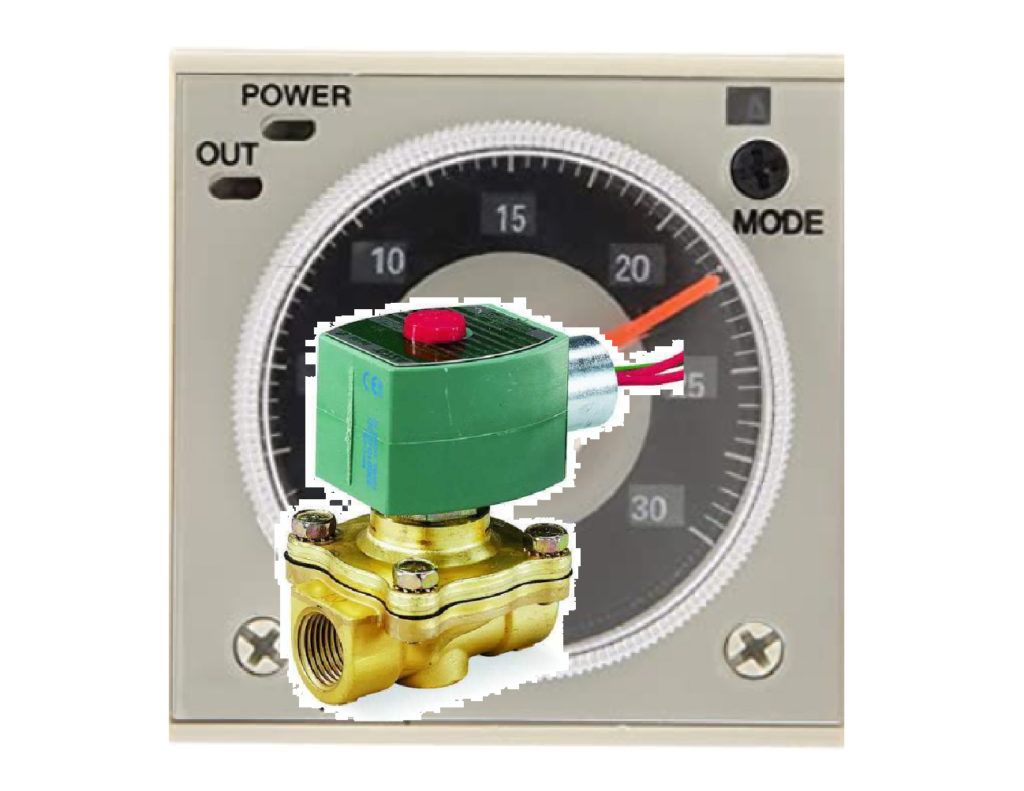
Virtually all HPDC dies are made with thermal passages. Usually the die is cooled by flowing water through these passages. (this discussion is not about hot oil or compressed air cooling) Most die cast machine installations include ball valves to start and stop water flow through the thermal passages. These ball valves prevent waster from continuing to flow while the die is being changed. Good die casters know that it is possible to reduce start up scrap by delaying the start of water flow until after a few warm up shots have occurred. If water start up is delayed too long the in rush of cold water may split the die inserts.
Die castings is a thermal process. The best result occur if every shot is the same. I wish to remove exactly the same amount of heat every cycle. Heat removal occurs when the water is flowing. The method is flow or no flow (it is not water or no water – this splits inserts) Water flows in my die thermal passages for a constant amount of time after each shot once warm up is complete
In this computer age I prefer to build in intelligence. The first step is finding a computer controlled valve to replace the ball valve. I normally do not recommend specific brands but ASCO diaphragm valves are the only one I have found suitable for the task. (Other seasoned HPDC practitioners are welcome to chime in if they have found other good brands) This may be related to the fact that were designed for fire protection sprinkler systems (ASCO is a contraction of American Sprinkler Company) Yes they cost twice as much as the knock offs) You may not able to run the valve with the machine control but that does not prevent adding cover and ejector ASCO valves run by old fashioned timers in the panel.
My best installations are run by the machine PLC and set using the HMI. They include program features to
- Avoid boiling in the die thermal passage
- Run dies with split inserts
- Allow 15 minute stops without incurring start up scrap
- Replace hot oil units
- Accelerate die warm up
Some machine builders like Buhler will configure new machines to include water timer control. Usually you need to specify that this is an option that you wish to purchase. I recommend a minimum of three (cover ejector & slides) separate valves.