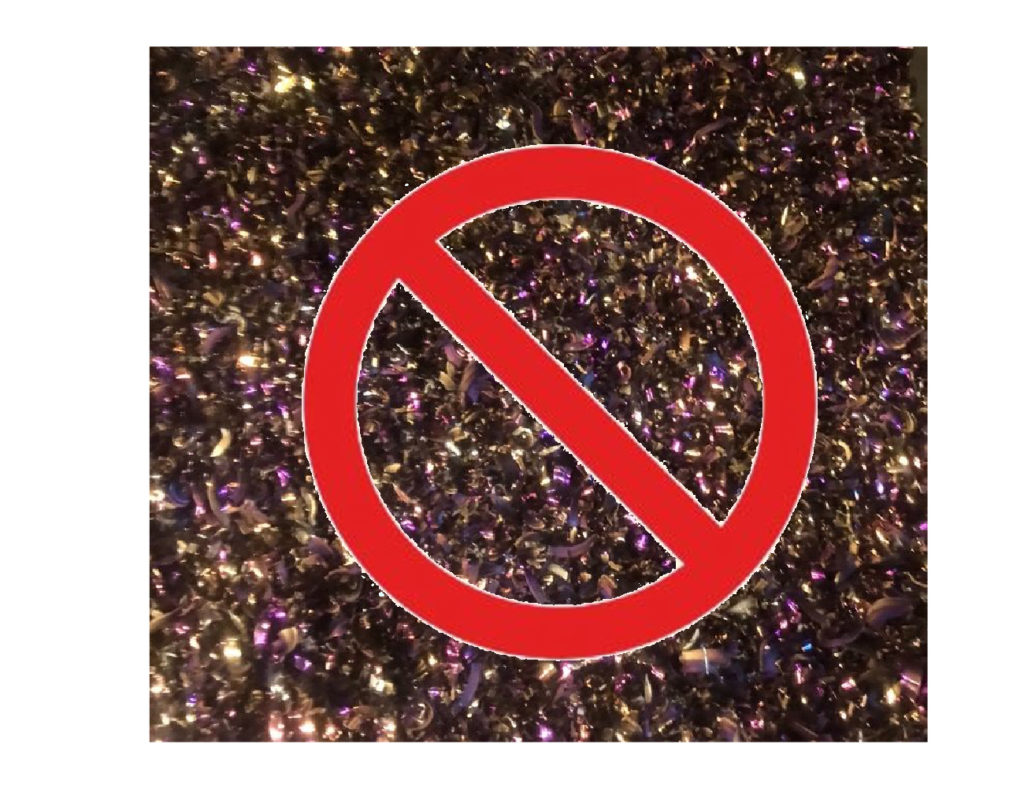
Shigeo Shingo was a leading expert in the Toyoda production system as a Japanese industrial engineer. Many current industrial best practices can be traced back to his teaching. This post is on on only one of his teachings. Manufacturing is more cost effective if you utilize processes that do not make chips. This sounds like an impossible command if you are a manufacturer who specializes in machining.
No Shingo was not trying to put all machining suppliers out of business. Some of the processes that machining houses perform can be accomplished chip free. Many chip free processes are the result of a tighter working relationship between the die caster and the machining house
- Cast chamfers or cast chamfers with counter bores can replace machined chamfers.
- Form taps can replace cut taps a) Form taps have 5 times the life b) Form taps tolerate some porosity in the bosses c) Structural alloys such as 356 need the work hardening of a form taps to achieve sufficiently strong threads
- Orbitformed cast studs can replace screwed connections
- Roll burnishing can solve microporosity in bores
- Welding is chip free
As die castings get larger we get more concerned about the foot print of the total operation. One of the nice things about chip free operations is that they can be accomplished in final assembly. Moving a part from station to station does not add value. It becomes possible to do less moves if the number of stations is reduced. This means that each station has more operations. Many of my more recent manufacturing cells implement chip tree operations such as form tapping in stations downstream of the CNC machining centers. I have discovered that a tapping head is less expensive per spindle when compared to a CNC machining center spindle